The Process of Making Leather
Leather is a natural byproduct of rearing animals for meat; when it comes in for processing it’s still in a raw form. There are several processes the hide must go through before it can even be called ‘leather’ at all. This process varies in different parts of the world, but it typically looks like this:
First, the hide is soaked in lime to remove bits like hair and unwanted proteins. Then unwanted bits are cut away (side trimmings), the hide is passed through a pair of rollers to regularize its thickness.
Now comes an important stage – splitting. Natural hide is too thick to be used in any product, so it is split horizontally into multiple layers. The topmost layer is called the top grain – it’s the most expensive and durable type of leather, but also the toughest to work with. The layer underneath is called the ‘split’. This material is softer, slightly easier to work with and is suitable for a variety of products.
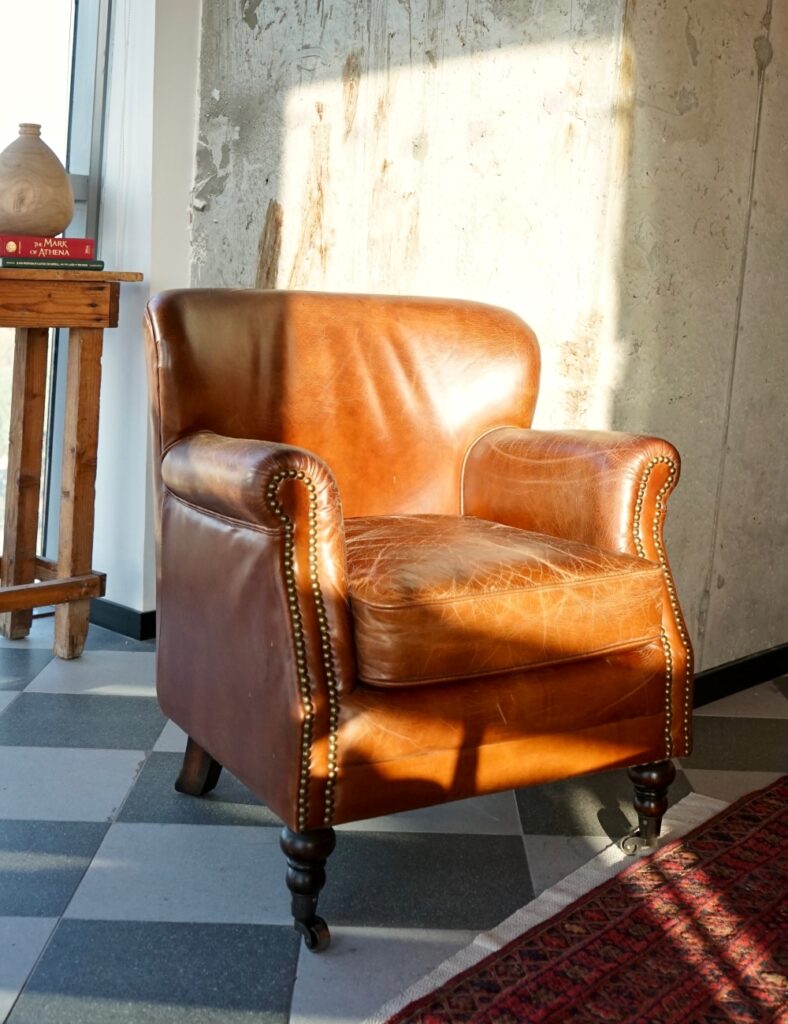
After this comes a stage we’ve all heard of – tanning. During this process, hides are put in wooden drums where tanning agents give them all the qualities you typically observe in the final product – durability, ability to withstand repetitive cycles of wet and dry, etc.
The tanned leather is wrung dry by another set of rollers, after which it usually looks greyish in colour. It is then graded and sorted by what product it will ultimately be. It is then put back in the tanner and this time it is dyed as well. A second drying process is conducted – either naturally (air drying at room temperature) or in a dryer.
Finally the leather is coated with a special paste called stucco and buffed lightly to make it look better. This process also fills up any naturally occurring imperfections – insect bites, scratches.
If leather is destined for a special product – say a crocodile or ostrich print – then it is embossed by a roller to give it that pattern.
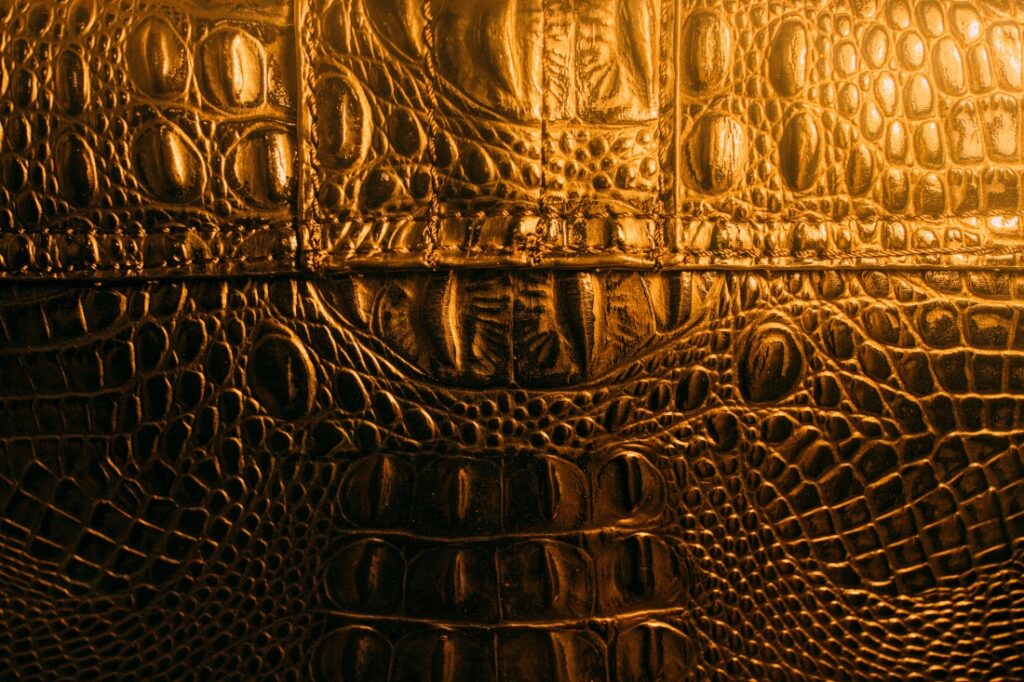
Some products require colours or textures that cannot directly be achieved on leather. For these the leather is coated with a thin film which can be of any colour.
In the old days, all tanneries involved heavy manual labour and required workers to dip their hands and feet in all sorts of chemicals. And toxic waste would be discarded carelessly into the nearest water body. Now in the modern era things have changed. Processes are automated, tanneries have pollution control units and don’t dump waste into rivers. The government even subsidizes the setup of these pollution-control units where there are leather industry clusters.
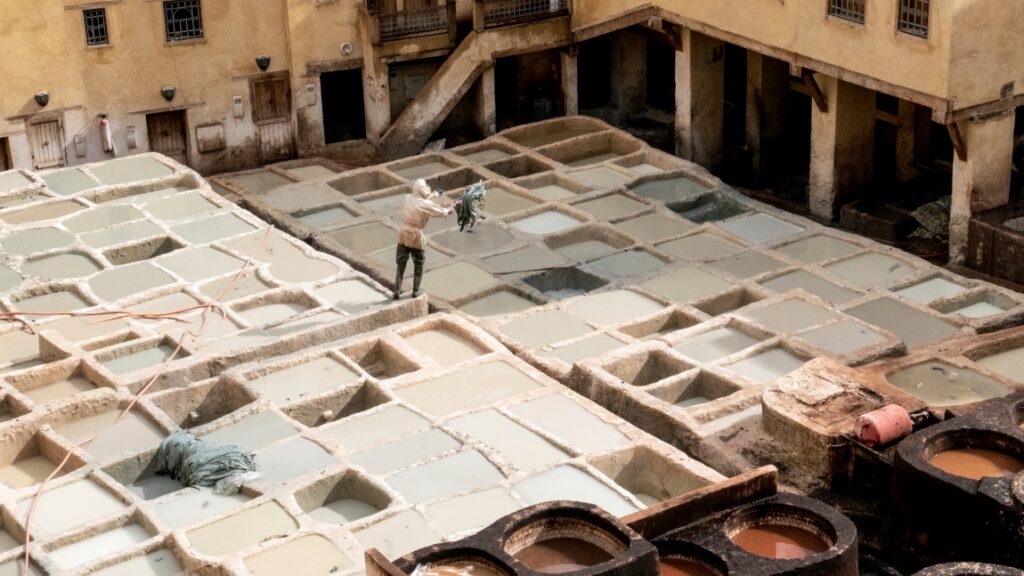